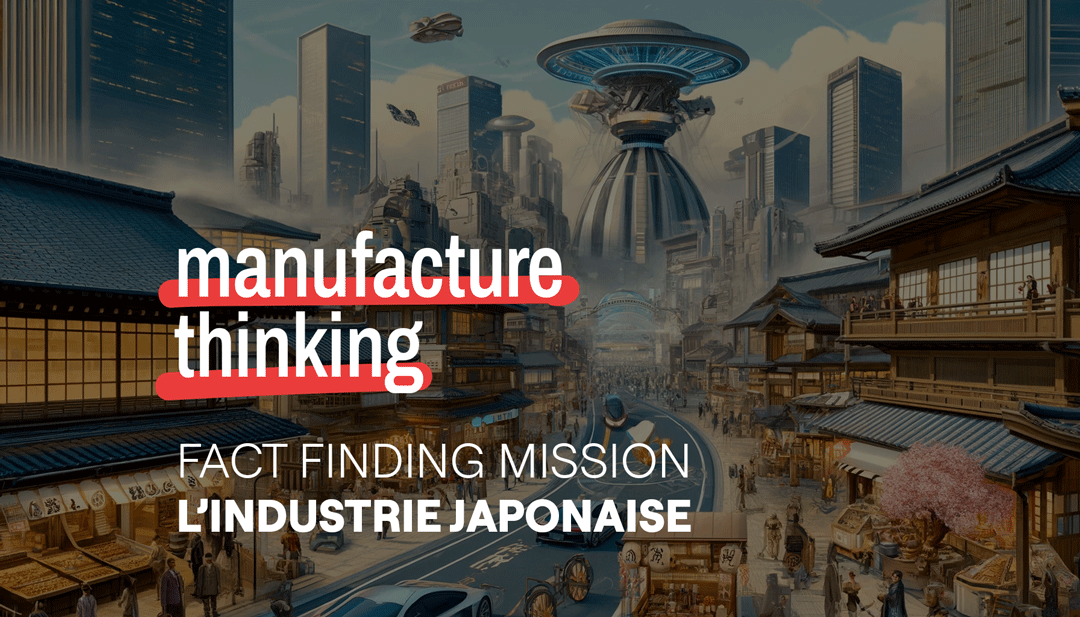
Japan: the factory in motion, at the heart of national priorities.
Plunging into the heart of Japanese industry, Manufacture Thinking explores the remarkable advances in automation, revealing the major trends and challenges in this booming sector.
A delegation of twenty members of the "Manufacture Thinking" Think Tank visited Japan from April 15 to 20, 2024 for an immersive discovery mission focused on the future of industry. The mission included a series of high-level meetings and company visits to explore developments in robotics, as well as a visit to the Swiss Embassy to discuss the role of Japanese industry in the global economy. The group also had the opportunity to visit iconic companies such as CASIO, FANUC and Bridgestone Robotics to understand state-of-the-art manufacturing and automation practices.
"Dark Factory: modern factories are autonomous
In Japan's advanced factories, robots take center stage, operating in a "dark" environment most of the time, lighting up only when they perform tasks requiring light; it's the robots that turn on the lights now. This near-complete automation means that quality tests can even be carried out at night, creating an unusual spectacle of robots in action in total darkness, and allowing humans to avoid the noise pollution associated with these tests. This evolution towards greater autonomy not only transforms production processes, but also redefines the concept of man-machine collaboration.
- Night-time testing: "biological" workers cannot bear to watch robot quality tests. The noise and heat induced by automatic testing prevent humans from attending. So the robots undergo their tests at night, in the dark of an unlit factory.
- Autonomy: in these advanced factories, robots build themselves, marking a significant step towards more complete autonomy.
- Co-botics: the association of man and machine, an ancient story brought up to date by the sensory capabilities of robots. An ever closer collaboration between man and machine, made safe by the use of force sensors.
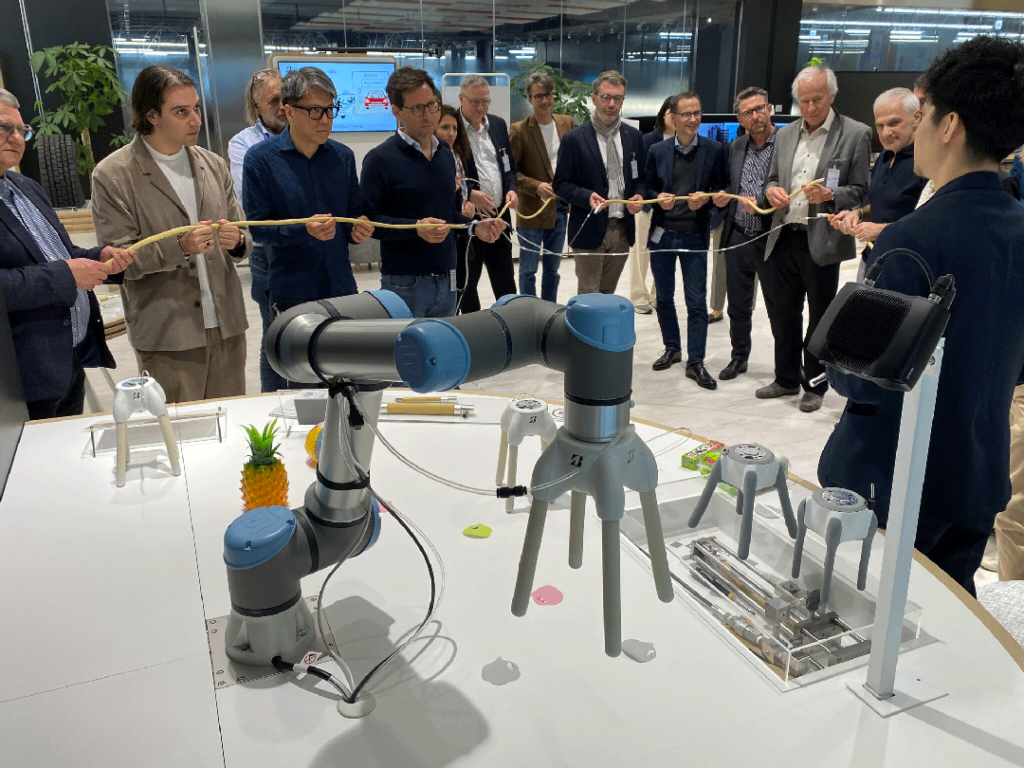
"Quality & Safety First": the influence of Japanese culture on industrial practices
The Japanese approach to quality and safety has a profound influence on industrial practices, from production to communication. This mentality favors strict quality control, encouraging integral value chain management. However, this approach may limit innovation in a constantly changing world, underlining the need for more open and collaborative models to foster innovation.
- Verticality: the focus on quality control encourages integral/vertical management of the value chain. In-house developments are favored. This model, adapted to a stable world, could limit innovation in an increasingly innovative industrial world. How can we move towards open, collaborative ecosystems in this context?
- Open innovation & young generation: Bridgestone is investing heavily in an open innovation hub where the new generation of engineers is beginning to explore tomorrow's technologies, products and business models. We were presented with a series of incipient and wildly free proposals. An interesting and fragile offshoot; to be continued.
- Trend towards automation: Japan, faced with an ageing population and a shortage of manpower, is increasingly turning to automation to compensate for this shortcoming.
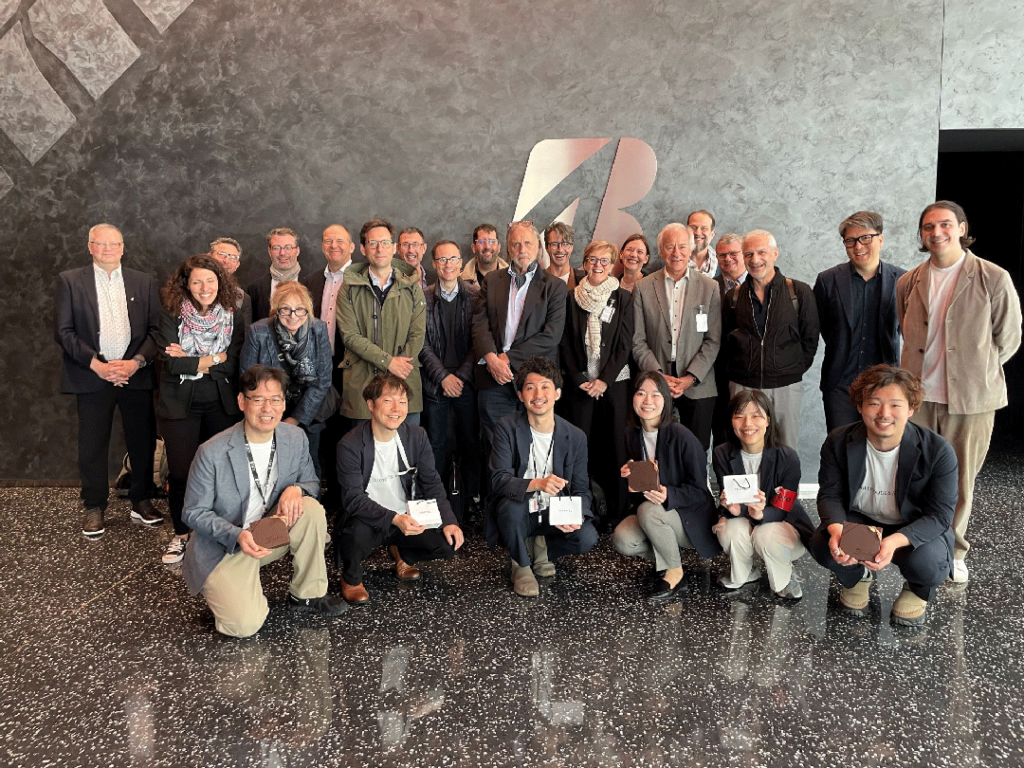
Engineering, a rapidly changing profession
Engineering is undergoing a rapid transformation. The progressive automation of manufacturing processes is having a major impact on design. Generative artificial intelligences are redefining the role of engineers by proposing innovative, optimized solutions based on innumerable, previously inaccessible and unusable data. This evolution towards two-headed "man-machine" co-design promises to revolutionize traditional engineering processes, paving the way for new design and production methods - faster, better, more creative.
- The policy of small steps: fully automated assembly lines are a slow, iterative process.
- The role of engineers: generative AI allows us to envisage a future in which engineering and design methods are entrusted to machines. Integrating production-related constraints, AIs will be able to investigate innumerable paths optimizing all design and engineering parameters. A major transformation is on the horizon, altering the role of engineers in quite astonishing ways.
- Design": industrial design extends its definition to include aesthetics, function, production and cost. Defining the objective, or the optimization function, will always be a matter of choice, since unlike in chess, the rules in industry are a matter of choice and are not immutable.
The soft era (Software vs. Hardware)
While innovation in modern factories is often associated with hardware and physical automation, it's surprising how little attention is paid to software and artificial intelligence in industrial discourse. Yet the development of an operating system to drive the factories of the future and the rise of generative AI are major challenges to be met. This trend raises questions about the future of automation and innovation in the industrial sector.
- Operating System: we're expecting the emergence of an OS to control the factories of tomorrow. Data collection and processing will be at the heart of these "flexible" factories. The programming, or self-programming, of robots requires the transfer of these assembly lines to software. This is a colossal and difficult challenge.
- The factory in motion: we can divide the evolution of factories into three key stages: automation, empowerment and verticalization. The first stage, automation, has already been achieved. The second stage, empowerment, is emerging thanks to AI agents, giving greater autonomy to the "artificial workers" of tomorrow's factories. The next stage, soft factories, is on the horizon. These factories, built on software and data, will not only manufacture autonomously, but will also take charge of design. The "verticalization" of the production process is underway. The factory is moving up a dimension.
An aging population and automation
Faced with an aging population and a shortage of manpower, Japan is increasingly turning to automation to compensate for this shortcoming. Innovation in robotics, with notable advances in sensory perception and object manipulation, is becoming a national issue. The "dark factory" concept and the emphasis on physical automation could be answers to this demographic challenge, underlining the growing importance of automation in Japan's industrial landscape.
- Versatile grippers: advances in robotics are focusing on the development of versatile grippers capable of handling a variety of objects, making automation more flexible and adaptable to changing production needs.
- National investment: the Japanese government actively supports research and development in the field of robotics, recognizing automation as a crucial means of maintaining economic competitiveness in the face of demographic challenges.
- Integration with industrial culture: automation is deeply integrated with Japanese industrial culture, with companies actively seeking to combine craft traditions with cutting-edge technologies to create innovative solutions that meet market needs.
Source: Manufacture Thinking
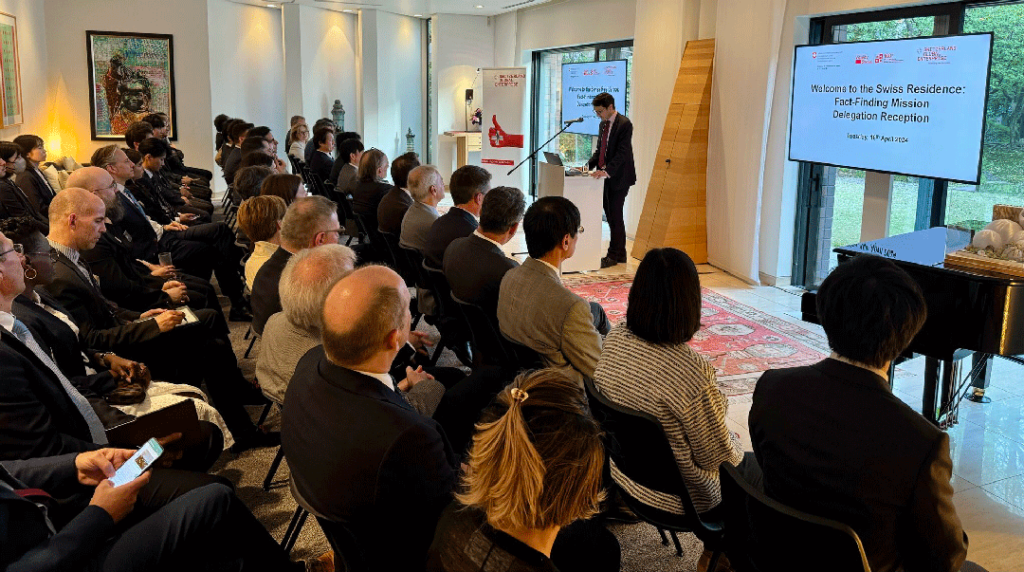
In order to see what is really happening on the ground, so-called "fact-finding" trips are organized on a regular basis, to visit key facilities and meet eminent people in different countries around the world.
www.manufacturethinking.ch